Home » Blog » Energy saving » MV motor starting current problems
MV motor starting current problems
Mill motor, 2.9MW, 6.3KV, rotor current: 775A, rotor voltage: 2770V
In this case sometimes we recorded 775A as starting current and in other times we recorded 400 A for rotor current during start and for stator the current is variable, in some case it was 85 A, and in other was larger than 400a. This motor starts with liquid starter.
Questions: what is your idea about differentiation? What is cause of current reduction? Is the liquid starter resistance variable during each case of start?
Rotor current will be directly proportional to torque and stator current. In affect we need to measure the stator current and calculate the approx rotor current. Measuring the rotor current directly with standard instruments will give errors as we are in affect measuring the current at whatever the slip frequency is.
For example, If the stator full load current was 250A (not sure what it is in this case) and the Stator start current was 400A (1.6x) then we would expect Rotor start current to be 1.6 x Rotor full load current = 775 x 1.6 = 1240A. Torque delivered would be around 1.6 x Full load torque, very typical for a ball mill or sag mill.
Correct measurement in the rotor current can be done with the likes of hall effect transducers or even shunts but not clamp-on ammeters unless they use hall affect or similar technology.
The liquid starter simply adds resistance in the rotor during starting to produce torque and depending on the electrode type and design, the start current and therefore torque should be similar with each new start. Generally the electrodes start wide open at start and slowly close up as the start progresses. Finally the rotor is then shorted as the motor gets to full speed and then runs like any cage motor. Differences in start current (eg as measured in the stator) would only be due to the electrode position at start being different each time. Liquid temperature will affect it only slightly.
The load will not vary the start current, only the resistance in the rotor and the speed of the rotor will affect that.
With no load the motor will be up to speed really quickly irrespective of the starting sequence time setting, and the measurements are probably picking up on start transients so appear somewhat random. So at no load we will not see the true performance and affect of the Liquid Resistance Starter as it is set up to deliver 1.5x FLT which we don't need for an unloaded start.
Sodium Carbonate electrolyte solution is commonly used in these starters at a recommended dose rate to give the start resistance and we just need to ensure the interlocks prevent starting unless the electrodes are in the open position.
By the way, the equivalent of DOL with a slip ring motor is electrodes shorted out which should not be possible with the control circuit. Also, this is not recommended due to extremely high inrush current with shorted slip rings.
This is in affect a simple device so we don't have any issues as long as the stator supply is solid and balanced and the slip rings of the motor are affect connected to the LRS.
Under a loaded start we will see everything will probably work OK and will have time to make the right measurements.
We can run a control system check without main power to ensure the electrodes are moving and the right sequence is in place.
In this case sometimes we recorded 775A as starting current and in other times we recorded 400 A for rotor current during start and for stator the current is variable, in some case it was 85 A, and in other was larger than 400a. This motor starts with liquid starter.
Questions: what is your idea about differentiation? What is cause of current reduction? Is the liquid starter resistance variable during each case of start?
Rotor current will be directly proportional to torque and stator current. In affect we need to measure the stator current and calculate the approx rotor current. Measuring the rotor current directly with standard instruments will give errors as we are in affect measuring the current at whatever the slip frequency is.
For example, If the stator full load current was 250A (not sure what it is in this case) and the Stator start current was 400A (1.6x) then we would expect Rotor start current to be 1.6 x Rotor full load current = 775 x 1.6 = 1240A. Torque delivered would be around 1.6 x Full load torque, very typical for a ball mill or sag mill.
Correct measurement in the rotor current can be done with the likes of hall effect transducers or even shunts but not clamp-on ammeters unless they use hall affect or similar technology.
The liquid starter simply adds resistance in the rotor during starting to produce torque and depending on the electrode type and design, the start current and therefore torque should be similar with each new start. Generally the electrodes start wide open at start and slowly close up as the start progresses. Finally the rotor is then shorted as the motor gets to full speed and then runs like any cage motor. Differences in start current (eg as measured in the stator) would only be due to the electrode position at start being different each time. Liquid temperature will affect it only slightly.
The load will not vary the start current, only the resistance in the rotor and the speed of the rotor will affect that.
With no load the motor will be up to speed really quickly irrespective of the starting sequence time setting, and the measurements are probably picking up on start transients so appear somewhat random. So at no load we will not see the true performance and affect of the Liquid Resistance Starter as it is set up to deliver 1.5x FLT which we don't need for an unloaded start.
Sodium Carbonate electrolyte solution is commonly used in these starters at a recommended dose rate to give the start resistance and we just need to ensure the interlocks prevent starting unless the electrodes are in the open position.
By the way, the equivalent of DOL with a slip ring motor is electrodes shorted out which should not be possible with the control circuit. Also, this is not recommended due to extremely high inrush current with shorted slip rings.
This is in affect a simple device so we don't have any issues as long as the stator supply is solid and balanced and the slip rings of the motor are affect connected to the LRS.
Under a loaded start we will see everything will probably work OK and will have time to make the right measurements.
We can run a control system check without main power to ensure the electrodes are moving and the right sequence is in place.
You may also like:
A more efficient variable speed drive for motors could help the ubiquitous, energy-sucking devices make another leap in energy efficiency. The problem is that most motors are oversized because of high torque ...
In a loop circuit in which the only component is a simple resistor, that resistor is the only thing in the loop that actually "resists" current flow. Apply a DC voltage to a loop without that resistance and ...
The key to know which motor is better to use on variable speed drives depends entirely on the individual application for which it will be used.
The key to picking the proper motor based on the answers to ...
A motor manufacturer assigns a RATING to the motor, which is put on the motor rating plate.( OR IN THE CATALOG)
As the rating plate mentions RATED output and RATED speed, RATED torque is derived from these.
With the continuous improvement of the technical level of textile machinery mechatronics, variable speed control has become a trend. Most textile machines apply variable speed drives in the AC induction motors.
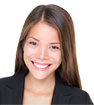
Hot Tags
Featured
7 months back I was involved in a harmonics evaluation study at Budweiser. This was one of many I've participated in over the past 20 years, basically because in facilities like ...
Most of variable speed drives are applying on high temperature fans, kiln head coal mill fans, kiln head surplus fans, raw mill circulating fans and so on. Two production lines ...
Variable speed drive application in purification system optimizes the system performance, improves purification effect, reduces power consumption greatly. According to related ...
The motor power factor does not make a big difference other than giving an idea of loading. In regards to the variable speed drive fixing power factor everyone is mostly correct. ...
A soft starter is a basic device which will ramp up the speed of your motor to full speed over a preset time, easing mechanical stress and also easing the high inrush currents ...
What's New
Variable Speed Drive Harmonics
Variable speed drive energy saving in cement industry
PLC and DAQ
Is it good to do preventive maintenance for variable speed drives
Does motor starts number affect motor life?
Variable speed drive for ID Fans in mining industry
Regenerative power frequency back to line power
Variable speed drive for axial-flow fans
Variable speed drive energy saving in cement industry
PLC and DAQ
Is it good to do preventive maintenance for variable speed drives
Does motor starts number affect motor life?
Variable speed drive for ID Fans in mining industry
Regenerative power frequency back to line power
Variable speed drive for axial-flow fans