A good motor with a good variable frequency drive can give 100% of nominal torque at 5% of rated speed, and sometimes at such speed torque should be also higher. If possible, take care to increase cooling not only by convection in air, but also by conduction to cool metal base or metal flange. You can also increase infrared emission using a treated motor surface to increase heat emission (Alumite finishing, or some black paints or treatments).
It has no issues using an oversized VFD. Assuming that's a voltage source drive (most common topology). This design manages the voltage and frequency to attain commanded speed. The current supplied to motor is only what is needed to magnetize the windings plus the torque producing current. In other words, the VFD is a 'current allower' and not a 'current pump'.
For variable frequency drive in continuous operation, we take an external visual inspection for the VFD running state. Regular inspect variable frequency drive to see if there is running anomalies or not, we have following methods:
Control circuit provides control signal to the asynchronous motor power supply (voltage and frequency adjustable) main circuit, which has the arithmetic circuit of frequency and voltage, the voltage and current detection circuit of the main circuit, the speed detecting circuit of the motor, the driving circuit of the operation control signal amplifier, and the protection circuit of the inverter and motor.
Derating, in general, is a little misunderstood. If a motor and variable frequency drive is in the same relative environment, derating of the variable frequency drive is not required. If you have a 10hp motor and VFD at sea level and then move them to, say, 10,000 feet, they derate together, so they still work together.
When choosing variable frequency drives for an application it's critical to know exactly the purpose intended. There are so many variables. A fan application although simple enough can have many factors that can complicate a motor if not correctly sized or programmed.
Most vector VFDs can handle a fan application but the key is selecting and sizing a drive for long term and that will pose no unwanted spikes or heat production on both electric motor and the VFD drive.
Most vector VFDs can handle a fan application but the key is selecting and sizing a drive for long term and that will pose no unwanted spikes or heat production on both electric motor and the VFD drive.
Successful rewinding of motors that are driven by variable speed drives does not rest on one large issue but in several small issues, all must be taken care of. I can only hope that the invention of variable speed drive will lead us back to the days when rewinding was a skilled trade.
With the continuous improvement of the technical level of textile machinery mechatronics, variable speed control has become a trend. Most textile machines apply variable speed drives in the AC induction motors.
Explaining some premature motor winding failures (multiple manufacturers) on VFD (multiple manufacturers) driven motors in high elevations. Some motors are VPI, all are inverter rated. Voltage varies from 460/480V - 575 and 690V. PWM varies from 1.5 - 3kHz. The failures are not seen at elevations below 3000M and the actual analysis of the failed motors are unreliable. Motors are appropriately derated for elevation in all cases.
Someone wants to upgrade his tomato packing plant so he installs VFDs on the motors that have been in service since 1963 when they were first installed. Run them on the new variable frequency drives and they fail in 12 months, (almost) every time.
The key to know which motor is better to use on variable speed drives depends entirely on the individual application for which it will be used.
The key to picking the proper motor based on the answers to these questions is to understand the difference between NEMA MG1 Part 30 which is titled "Application Considerations for Constant Speed Motors Used on a Sinusoidal Bus with Harmonic Content and General Purpose Motors Used with Adjustable-Voltage or Adjustable-Frequency Controls or Both" and NEMA MG1 Part 31 which is titled "Definite-Purpose Inverter-Fed Polyphase Motors".
The key to picking the proper motor based on the answers to these questions is to understand the difference between NEMA MG1 Part 30 which is titled "Application Considerations for Constant Speed Motors Used on a Sinusoidal Bus with Harmonic Content and General Purpose Motors Used with Adjustable-Voltage or Adjustable-Frequency Controls or Both" and NEMA MG1 Part 31 which is titled "Definite-Purpose Inverter-Fed Polyphase Motors".
DC Motor now a days mostly used for precise speed control of Motor Application,in order to replace the DC motor with AC Induction Motor keep in mind that the initial Torque of the Motor of Load to be Calculate which is to be drive and then fix it the RPM side.
DC motor replace with AC motor its depend on application, some DC motors replace with same rating and some time higher then but mostly there is no issue replace with same motor.
DC motor replace with AC motor its depend on application, some DC motors replace with same rating and some time higher then but mostly there is no issue replace with same motor.
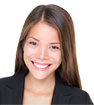
Hot Tags
Featured
7 months back I was involved in a harmonics evaluation study at Budweiser. This was one of many I've participated in over the past 20 years, basically because in facilities like ...
Most of variable speed drives are applying on high temperature fans, kiln head coal mill fans, kiln head surplus fans, raw mill circulating fans and so on. Two production lines ...
Variable speed drive application in purification system optimizes the system performance, improves purification effect, reduces power consumption greatly. According to related ...
The motor power factor does not make a big difference other than giving an idea of loading. In regards to the variable speed drive fixing power factor everyone is mostly correct. ...
A soft starter is a basic device which will ramp up the speed of your motor to full speed over a preset time, easing mechanical stress and also easing the high inrush currents ...
What's New
Variable Speed Drive Harmonics
Variable speed drive energy saving in cement industry
PLC and DAQ
Is it good to do preventive maintenance for variable speed drives
Does motor starts number affect motor life?
Variable speed drive for ID Fans in mining industry
Regenerative power frequency back to line power
Variable speed drive for axial-flow fans
Variable speed drive energy saving in cement industry
PLC and DAQ
Is it good to do preventive maintenance for variable speed drives
Does motor starts number affect motor life?
Variable speed drive for ID Fans in mining industry
Regenerative power frequency back to line power
Variable speed drive for axial-flow fans