To compete with the same applications with induction or PM machines with lower pole numbers, axial gap topologies generally require higher carrier frequencies in the variable speed drive that feed. This is to minimize ripple in the current waveforms and the resulting torque ripple at the shaft. The VSD drive size tends to be larger to accommodate the switching losses at the higher PWM carrier frequencies.
VFD is for controlling the speed of a motor which is under load, by changing the frequency of applied voltage. When your production line needs the motor to produce lower power, with the same torque it had before, its speed should be lowered by decreasing the frequency of applied voltage, this makes the impedance of the motor decrease and in turn, the amount of applied voltage comes lower and power consumption comes lower.
A soft starter is a basic device which will ramp up the speed of your motor to full speed over a preset time, easing mechanical stress and also easing the high inrush currents which can be experienced by starting a motor under load. A breaker will cut the supply to your motor if the load is too high. A VFD will allow you to control a motor (to varying degrees of accuracy depending on the model selected) by varying the phase angle (amongst other things). It will give you the most control over your motor including at the most basic ramp time running speed.
One of the ways these days that i check this process is by observing the winding process. By understanding the winding environment and not assuming anything, By taking part actively in DFM. By seeing what happens in production and making changes that seem easy to me but may seem very difficult to people on the floor.
It involves my proprietary power electronics, DC machines working in concert with AC grids, bi-directionally blocking the traditional amp draws of the AC grid and bi-directionally permitting forward emf generation as the DC machine armatures rotate counter clock-wise at their drive ends. All working in concert with each other to perform useful work under load as negative electricity powered electric engines. The torque dynamics are all the mirror image of traditional torque dynamics, because we have discovered that "rotational thrust" is "relative" in terms of its action and reaction effects.
Due to current decrement in the Generator during fault conditions the Back-up protection with IDMT relay for a generator in the Electrical protection Scheme becomes complicated. Accordingly, the setting of the associated IDMT relay is set in such way that the said relay will not operate for a system fault but will respond when fault current is fed into the Generator which acts as a back-up to the main Generator Protection.
Through transformer you have flows of active and reactive power on their way to consumer, so you need to know quantity of power (active and reactive) which flows through transformer.
SV-PWM is actually just a modulation algorithm which translates phase voltage (phase to neutral) references, coming from the controller, into modulation times/duty-cycles to be applied to the PWM peripheral.
It is a general technique for any three-phase load, although it has been developed for motor control.
SV-PWM maximizes DC bus voltage exploitation and uses the "nearest" vectors, which translates into a minimization of the harmonic content.
It is a general technique for any three-phase load, although it has been developed for motor control.
SV-PWM maximizes DC bus voltage exploitation and uses the "nearest" vectors, which translates into a minimization of the harmonic content.
The application will drive the choice of gear motor. If you go with brush DC motors you will save money but have a lot of maintenance. If you go brushless motor it costs more but last much longer.
The more detail you have about your application the better. Knowing exactly, in engineering terms, what your requirements are can save you a bunch of money.
The more detail you have about your application the better. Knowing exactly, in engineering terms, what your requirements are can save you a bunch of money.
For simulink PMSM model, you'll have to determine if your motor is salient or non-salient one.. and other important parameters. Once you understand the Space-Vector theory you wouldn't even need the variable frequency drive (just generate the voltage vectors yourself), at least for first evaluation. however, if you do want to use the simpower blocks for the VFD, that'll be tricky (to connect the realized equations in simulink to simpower blocks).
In this case sometimes we recorded 775A as starting current and in other times we recorded 400 A for rotor current during start and for stator the current is variable, in some case it was 85 A, and in other was larger than 400a. This motor starts with liquid starter.
Questions: what is your idea about differentiation? What is cause of current reduction? Is the liquid starter resistance variable during each case of start?
Questions: what is your idea about differentiation? What is cause of current reduction? Is the liquid starter resistance variable during each case of start?
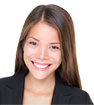
Hot Tags
Featured
7 months back I was involved in a harmonics evaluation study at Budweiser. This was one of many I've participated in over the past 20 years, basically because in facilities like ...
Most of variable speed drives are applying on high temperature fans, kiln head coal mill fans, kiln head surplus fans, raw mill circulating fans and so on. Two production lines ...
Variable speed drive application in purification system optimizes the system performance, improves purification effect, reduces power consumption greatly. According to related ...
The motor power factor does not make a big difference other than giving an idea of loading. In regards to the variable speed drive fixing power factor everyone is mostly correct. ...
A soft starter is a basic device which will ramp up the speed of your motor to full speed over a preset time, easing mechanical stress and also easing the high inrush currents ...
What's New
Variable Speed Drive Harmonics
Variable speed drive energy saving in cement industry
PLC and DAQ
Is it good to do preventive maintenance for variable speed drives
Does motor starts number affect motor life?
Variable speed drive for ID Fans in mining industry
Regenerative power frequency back to line power
Variable speed drive for axial-flow fans
Variable speed drive energy saving in cement industry
PLC and DAQ
Is it good to do preventive maintenance for variable speed drives
Does motor starts number affect motor life?
Variable speed drive for ID Fans in mining industry
Regenerative power frequency back to line power
Variable speed drive for axial-flow fans