Home » Blog » Energy saving » The definition of Space Vector PWM (SVPWM)
The definition of Space Vector PWM (SVPWM)
SV-PWM is actually just a modulation algorithm which translates phase voltage (phase to neutral) references, coming from the controller, into modulation times/duty-cycles to be applied to the PWM peripheral.
It is a general technique for any three-phase load, although it has been developed for motor control.
SV-PWM maximizes DC bus voltage exploitation and uses the "nearest" vectors, which translates into a minimization of the harmonic content.
The classical application of SV-PWM is vector motor control, which is based on the control of currents' projection on two orthogonal coordinates (direct and quadrature, dq), called Field Oriented Control (FOC). For induction machines, the most common choices for the direct axis is to align it to the rotor field (rotor FOC) or to the stator field (stator FOC).
The basic concept is that with a known motor and known voltage output pulses you can accurately determine rotor slip by monitoring current and phase shift. The controller can then modify the PWM "sine" wave shape, frequency or amplitude to achieve the desired result.
For example the desired speed is 200 rpm and the control senses there is 2 rpm of slip so it increases the frequency slightly to bring the speed up. Since torque can also be determined it can also be controlled.
SVPWM just does a lot of sampling, calculating and wave form manipulation. The specific algorithms and deciding what the best output solution is for different situations could fill up several books.
SV means space vector, as in space vector modulation. SVM basically allows a 3-phase bridge PWM drive to supply about 15% higher peak voltage to a motor than the standard sine-triangle modulation scheme by allowing the neutral point of the motor to move away from the nominal 1/2 of the supply rail (it will look like a triangle wave). The characteristic voltage output of an SVM-modulated sine wave is a sine wave with a double-hump on the peaks.
To be more precise, SVM output about 15% more "non over-modulated" voltage than the traditional carrier based PWM. That is the maximum voltage before over-modulation happens. The shape of the phase voltage has a double-hump as mentioned (similar to a standard PWM + third harmonic addition). The line-to-line voltage will not show the humps though.
See a space vector control drive here.
It is a general technique for any three-phase load, although it has been developed for motor control.
SV-PWM maximizes DC bus voltage exploitation and uses the "nearest" vectors, which translates into a minimization of the harmonic content.
The classical application of SV-PWM is vector motor control, which is based on the control of currents' projection on two orthogonal coordinates (direct and quadrature, dq), called Field Oriented Control (FOC). For induction machines, the most common choices for the direct axis is to align it to the rotor field (rotor FOC) or to the stator field (stator FOC).
The basic concept is that with a known motor and known voltage output pulses you can accurately determine rotor slip by monitoring current and phase shift. The controller can then modify the PWM "sine" wave shape, frequency or amplitude to achieve the desired result.
For example the desired speed is 200 rpm and the control senses there is 2 rpm of slip so it increases the frequency slightly to bring the speed up. Since torque can also be determined it can also be controlled.
SVPWM just does a lot of sampling, calculating and wave form manipulation. The specific algorithms and deciding what the best output solution is for different situations could fill up several books.
SV means space vector, as in space vector modulation. SVM basically allows a 3-phase bridge PWM drive to supply about 15% higher peak voltage to a motor than the standard sine-triangle modulation scheme by allowing the neutral point of the motor to move away from the nominal 1/2 of the supply rail (it will look like a triangle wave). The characteristic voltage output of an SVM-modulated sine wave is a sine wave with a double-hump on the peaks.
To be more precise, SVM output about 15% more "non over-modulated" voltage than the traditional carrier based PWM. That is the maximum voltage before over-modulation happens. The shape of the phase voltage has a double-hump as mentioned (similar to a standard PWM + third harmonic addition). The line-to-line voltage will not show the humps though.
See a space vector control drive here.
You may also like:
It involves my proprietary power electronics, DC machines working in concert with AC grids, bi-directionally blocking the traditional amp draws of the AC grid and bi-directionally permitting forward emf ...
Altitude Standard motors are designed to operate below 3300 feet. Air is thinner and heat is not dissipated as quickly above 3300 feet. Most motors must be derated for altitude. The following chart gives ...
AC reactors reduce harmonics, mitigates transient conditions and helps to maintain proper phase to phase voltages. DC reactors will also mitigate harmonics however it will provide more harmonic attenuation ...
Clean the variable frequency drive heatsink and check or replace the fans. I like new fans every five years. I also double check the drives installation. This is a good opportunity to make corrections to the ...
1a. if the driver is a synchronous motor there isn't a power factor problem as the motor will be either 1.0 or leading PF
1b. if the driver is induction: check with the motor manufacturer for the power ...
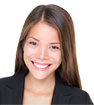
Hot Tags
Featured
7 months back I was involved in a harmonics evaluation study at Budweiser. This was one of many I've participated in over the past 20 years, basically because in facilities like ...
Most of variable speed drives are applying on high temperature fans, kiln head coal mill fans, kiln head surplus fans, raw mill circulating fans and so on. Two production lines ...
Variable speed drive application in purification system optimizes the system performance, improves purification effect, reduces power consumption greatly. According to related ...
The motor power factor does not make a big difference other than giving an idea of loading. In regards to the variable speed drive fixing power factor everyone is mostly correct. ...
A soft starter is a basic device which will ramp up the speed of your motor to full speed over a preset time, easing mechanical stress and also easing the high inrush currents ...
What's New
Variable Speed Drive Harmonics
Variable speed drive energy saving in cement industry
PLC and DAQ
Is it good to do preventive maintenance for variable speed drives
Does motor starts number affect motor life?
Variable speed drive for ID Fans in mining industry
Regenerative power frequency back to line power
Variable speed drive for axial-flow fans
Variable speed drive energy saving in cement industry
PLC and DAQ
Is it good to do preventive maintenance for variable speed drives
Does motor starts number affect motor life?
Variable speed drive for ID Fans in mining industry
Regenerative power frequency back to line power
Variable speed drive for axial-flow fans