Home » Blog » Motor control » What is the reason causes motor tripped?
What is the reason causes motor tripped?
You might want to look at the application and see if the motor was properly designed for your application. Obtain a load curve from the pump manufacturer under your typical site conditions (ie temperature, pressure, etc.) Also obtain a curve for worst case conditions. Send both curves to the motor manufacturer and tell them that you want to start the load with a Soft Starter. First ask them if the load can be started with a 65% voltage tap. Ask for a starting torque curve for 65%. Ask if the load can be started with limiting the current to 400%(389amp x 4 = 1556amp). Ask for a starting torque curve limiting current to 400%. Compare the results and see if there is sufficient torque to start the load and sufficient torque margin. Assuming you have not found a problem with the torque. Ask for a time vs current curve under all the conditions as stated above. You will need these curves to properly setup and coordinate your relaying.
Usually overcurrent (more than the starting current) or long time with starting current can make trip in starting, for some different problems (mechanical or electrical).
Was the speed zero or no when the protection trips?
If the problem is the mechanical load (as high load torque or inertia/viscosity of the load) the starting current value will be normal, but will maintain during long time and it can be a problem, maybe adjust the time to trip. The soft-starter voltage and or current limitation settings must be in according to the required acceleration time, too.
Which device provided the command to trip? A soft starter internal protection or an external relay gives the trip? If the soft-starter gives the trip, usually it has a display and show a code number of the error on trip and you can check it in a soft-starter manual.
First I suggest you to check the settings of the protections that gives the command to trip (soft-starter or relay).
Another cause assuming reduced voltage start, star/delta, autotransformer, primary resistance, soft start etc., could be that the motor is not delivering torque sufficient to accelerate the connected load to speed. That is the starting current and starting time under RVS conditions exceeds that permissible by the overload curve. A more advanced protection strategy such as motor thermal modeling may be required. Motor thermal modeling allows the user to 'match' the curves of the protection device to the connected motor.
If the motor is taking three phase balance overcurrent than most of the time it is seeing heavy overloading. The only electrical condition in which it will take that heavy balanced overcurrent is the one in which the winding are partially burnt but showing balance resistance in all three phases, which is highly unusual. Your information is incomplete. If you give more information on current pattern and the terminal voltage then I would be able to comment on it more.
Usually overcurrent (more than the starting current) or long time with starting current can make trip in starting, for some different problems (mechanical or electrical).
Was the speed zero or no when the protection trips?
If the problem is the mechanical load (as high load torque or inertia/viscosity of the load) the starting current value will be normal, but will maintain during long time and it can be a problem, maybe adjust the time to trip. The soft-starter voltage and or current limitation settings must be in according to the required acceleration time, too.
Which device provided the command to trip? A soft starter internal protection or an external relay gives the trip? If the soft-starter gives the trip, usually it has a display and show a code number of the error on trip and you can check it in a soft-starter manual.
First I suggest you to check the settings of the protections that gives the command to trip (soft-starter or relay).
Another cause assuming reduced voltage start, star/delta, autotransformer, primary resistance, soft start etc., could be that the motor is not delivering torque sufficient to accelerate the connected load to speed. That is the starting current and starting time under RVS conditions exceeds that permissible by the overload curve. A more advanced protection strategy such as motor thermal modeling may be required. Motor thermal modeling allows the user to 'match' the curves of the protection device to the connected motor.
If the motor is taking three phase balance overcurrent than most of the time it is seeing heavy overloading. The only electrical condition in which it will take that heavy balanced overcurrent is the one in which the winding are partially burnt but showing balance resistance in all three phases, which is highly unusual. Your information is incomplete. If you give more information on current pattern and the terminal voltage then I would be able to comment on it more.
You may also like:
VFD is for controlling the speed of a motor which is under load, by changing the frequency of applied voltage. When your production line needs the motor to produce lower power, with the same torque it had ...
But, compare with imported variable frequency drives, China domestic VFD's technologies need to take some time to catch up. Although in recent years the use of localization VFD brands have some advantages, but ...
Here I have very basic questions which I couldn't get when I searched in internet or in books. I am very new to my profession not aware of these things which I often face in my work. Please spend some time for ...
There will be little fall in the running torque supplied by the motor within the working voltage range of the motor and so the mechanical output and hence the electrical input remains practically same. The ...
but the inverters must have a common controller. In other words both inverters are controlled by a single system. That isn't specifically 2 separate variable frequency drives on one motor. but similar. ...
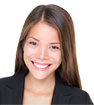
Hot Tags
Featured
7 months back I was involved in a harmonics evaluation study at Budweiser. This was one of many I've participated in over the past 20 years, basically because in facilities like ...
Most of variable speed drives are applying on high temperature fans, kiln head coal mill fans, kiln head surplus fans, raw mill circulating fans and so on. Two production lines ...
Variable speed drive application in purification system optimizes the system performance, improves purification effect, reduces power consumption greatly. According to related ...
The motor power factor does not make a big difference other than giving an idea of loading. In regards to the variable speed drive fixing power factor everyone is mostly correct. ...
A soft starter is a basic device which will ramp up the speed of your motor to full speed over a preset time, easing mechanical stress and also easing the high inrush currents ...
What's New
Variable Speed Drive Harmonics
Variable speed drive energy saving in cement industry
PLC and DAQ
Is it good to do preventive maintenance for variable speed drives
Does motor starts number affect motor life?
Variable speed drive for ID Fans in mining industry
Regenerative power frequency back to line power
Variable speed drive for axial-flow fans
Variable speed drive energy saving in cement industry
PLC and DAQ
Is it good to do preventive maintenance for variable speed drives
Does motor starts number affect motor life?
Variable speed drive for ID Fans in mining industry
Regenerative power frequency back to line power
Variable speed drive for axial-flow fans