For variable speed drives, there are two power semiconductor technologies employed: bridge rectifier and the output stage.
The bridge rectifier is made up of power rectifiers which are connected directly to the supply and drive a capacitor bank, either directly or via inductors. By design, then, the rectifier of the variable speed drive is less likely to be damaged by a short circuit on the output or in the motor.
In electronic design, they use "time simulation" (or "dynamic simulation"), which is an off-line calculation of how a system might respond to various inputs. The inputs are mathematical in this case, and the simulation need not run in real-time. Indeed, in the old days it might take days of calculation to get the result, even if the real process was very brief. In electronics, these are termed "SPICE models". My work long ago with CSMP and analog computers was similar. Calculating physics events like nuclear or chemical reactions, or weather models is similar.
The SCADA (Supervisory Control And Data Acquisition) would also be a HMI (Human Machine Interface) and if the HMI system had the additional data acquisition which most are capable of then it would also be SCADA. The advent of the Windows data exchange and client - server model has blurred the picture to the point this this question is bordering on being trivial as the differences are so small. The same questions could be asked or made about the differences in DCS and SCADA and HMI.
Advancements in industrial Ethernet switching technology have greatly improved the reliability in Ethernet communication. With the automation industry rapidly transitioning to Ethernet as a communication standard, it is vital that variable speed drive systems do the same. Products now are helping to lead this transition by providing an Ethernet process controller for new and existing variable speed drive systems.
say there is a permanent fault on overhead transmission line, the distance / line differential protection should operate and trip respect circuit breaker (CB) which is feeding the fault. This protection relay will initiate a 2 stage breaker failure (BF) relay too.
The motor power factor does not make a big difference other than giving an idea of loading. In regards to the variable speed drive fixing power factor everyone is mostly correct. A variable speed drive will always show a DPF (Displacement Power Factor) near unity. DPF is what a utility company traditionally monitors and is the measure of lag looking at current and voltage of power at 60hz or fundamental only. The true power factor on a VFD will change with loading etc and includes current and voltage inclusive of harmonics.
There will be little fall in the running torque supplied by the motor within the working voltage range of the motor and so the mechanical output and hence the electrical input remains practically same. The constant power concept is for practical purposes, as a thumb rule for frequency control like by variable speed drive.
In theory variable speed drive (VSD) is able to reduce the motor starting current at very low values is a fact that motor has limitations. I have seen many motors to stall because someone limited the starting current to a very low value. That low value is an argument to sell the equipment. Limiting the starting current depends on the type of motor and load operation curve reflected at motor shaft, for example a pumping system has a different curve than a conveyor and each application needs different starting torque and current.
For instance, let's take a transformer for an example. You test a transformer and you get short-circuit and open-circuit impedances and losses. Then, the most basic model for such transformer is a T circuit, with series RL impedances (R and X) for each winding, with a central magnetizing shunt branch usually represented by parallel-connected R and L (G and B for their conductance and susceptance, respectively).
The proper operation of an AC system requires magnetization/energization of the apparatus, machines, transformers, lines, etc.
If you do not properly energize the equipment, no active power conversion, MW conversion, (mechanical power being converted to electrical power in generators, electrical power being converted to mechanical power in motors, etc.) can happen. Similarly, you cannot transfer active power from one winding of a transformer to another winding, without first building up the magnetic flux at the core of said transformer.
If you do not properly energize the equipment, no active power conversion, MW conversion, (mechanical power being converted to electrical power in generators, electrical power being converted to mechanical power in motors, etc.) can happen. Similarly, you cannot transfer active power from one winding of a transformer to another winding, without first building up the magnetic flux at the core of said transformer.
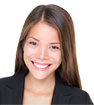
Hot Tags
Featured
7 months back I was involved in a harmonics evaluation study at Budweiser. This was one of many I've participated in over the past 20 years, basically because in facilities like ...
Most of variable speed drives are applying on high temperature fans, kiln head coal mill fans, kiln head surplus fans, raw mill circulating fans and so on. Two production lines ...
Variable speed drive application in purification system optimizes the system performance, improves purification effect, reduces power consumption greatly. According to related ...
The motor power factor does not make a big difference other than giving an idea of loading. In regards to the variable speed drive fixing power factor everyone is mostly correct. ...
A soft starter is a basic device which will ramp up the speed of your motor to full speed over a preset time, easing mechanical stress and also easing the high inrush currents ...
What's New
Variable Speed Drive Harmonics
Variable speed drive energy saving in cement industry
PLC and DAQ
Is it good to do preventive maintenance for variable speed drives
Does motor starts number affect motor life?
Variable speed drive for ID Fans in mining industry
Regenerative power frequency back to line power
Variable speed drive for axial-flow fans
Variable speed drive energy saving in cement industry
PLC and DAQ
Is it good to do preventive maintenance for variable speed drives
Does motor starts number affect motor life?
Variable speed drive for ID Fans in mining industry
Regenerative power frequency back to line power
Variable speed drive for axial-flow fans