Home » Blog » Questions & Answers » Motor networking control
Motor networking control
In the days before networked motors, all inputs were accounted for in the Input list and all outputs were accounted for in the Output list. The IO count was then evaluated to help determine the complexity of a system. IO counts directly impacted many various costs in the project such as cost of hardware, cost of wiring, and the cost of installation. The complexity of the system was used to estimate how much engineering time would be required for the project.
Networking of devices (MCCs as well as valves and instruments) makes the task of estimating a project much less straightforward.
1. "Smart MCC" implies the use of some type of network which supports each individual motor, whether a "two-state on/off" motor, "three-state off/forward/reverse motor" or "variable speed drive".
With each motor device, certain components which were traditionally discrete IO points are now wired at the motor controller itself component and communicated to the control system via the network. Common components include the "bucket disconnect", the "running status", and the "overload status". Therefore, your IO count may be less in a networked environment, but the complexity of the control may actually be greater.
2. Automatic Change over between running and standby motors
I interpret this as being a requirement to automatically switch from the normal motor to its designated backup when some type of fault is detected. If so, then you must somehow account for this in your motor list, MCC design, and complexity of the control system.
3. Dry run Protection
Sounds like an interlock for pumps to prevent running if the liquid level in the supply tank is below a safe level.
If so, then you may be quoting things which you are not qualified to do. This is not an "instrumentation" issue or an "electrical" issue, but rather a "process knowledge" issue.
4. Variable speed drives
If your MCCs are "smart", then these parameters are communicated over the network and you no longer need speed reference signals (analog outputs to the variable speed drive) or speed feedback signals (analog inputs from the drive)
5. Various trips (from DCS and SIS) that are coming to motors.
What is required for controlling the motor? I have never worked with SISs (Safety Instrumented Systems), but have used "safety relays" in motor controls which impacted wiring details without impacting "IO count".
You need to understand the requirements in order to quote or design the system -- Period.
6. There is only Local start and no DCS start.
It sounds like some motors have a local start button which is a "Manual" function, not an "Automatic" function. If so, there is probably a discrete input for this function.
Bear in mind that there may be also be a local Hand-Off-Auto selector switch for certain motors. If so, the Hand position and the Auto position require discrete inputs to the control system.
7. Apart from this I have considered few DI's for MCC Incomer's open or closed status.
Is it about the status of MCC Main Circuit Breakers? Does each motor "bucket" have an auxiliary switch to monitor its status? If so, these are often wired to the "smart motor" so that their status is communicated via the network rather than using discrete inputs. This cuts down on "IO count", but does not cut down on "complexity".
8. Interposing Relays
Interposing Relays are used when the amperage requirements of the final motor starter coil exceed the available amperage rating of the "first line" output device. This is a function of the hardware and how you propose to control the motors and must be addressed on a case-by case basis.
Networking of devices (MCCs as well as valves and instruments) makes the task of estimating a project much less straightforward.
1. "Smart MCC" implies the use of some type of network which supports each individual motor, whether a "two-state on/off" motor, "three-state off/forward/reverse motor" or "variable speed drive".
With each motor device, certain components which were traditionally discrete IO points are now wired at the motor controller itself component and communicated to the control system via the network. Common components include the "bucket disconnect", the "running status", and the "overload status". Therefore, your IO count may be less in a networked environment, but the complexity of the control may actually be greater.
2. Automatic Change over between running and standby motors
I interpret this as being a requirement to automatically switch from the normal motor to its designated backup when some type of fault is detected. If so, then you must somehow account for this in your motor list, MCC design, and complexity of the control system.
3. Dry run Protection
Sounds like an interlock for pumps to prevent running if the liquid level in the supply tank is below a safe level.
If so, then you may be quoting things which you are not qualified to do. This is not an "instrumentation" issue or an "electrical" issue, but rather a "process knowledge" issue.
4. Variable speed drives
If your MCCs are "smart", then these parameters are communicated over the network and you no longer need speed reference signals (analog outputs to the variable speed drive) or speed feedback signals (analog inputs from the drive)
5. Various trips (from DCS and SIS) that are coming to motors.
What is required for controlling the motor? I have never worked with SISs (Safety Instrumented Systems), but have used "safety relays" in motor controls which impacted wiring details without impacting "IO count".
You need to understand the requirements in order to quote or design the system -- Period.
6. There is only Local start and no DCS start.
It sounds like some motors have a local start button which is a "Manual" function, not an "Automatic" function. If so, there is probably a discrete input for this function.
Bear in mind that there may be also be a local Hand-Off-Auto selector switch for certain motors. If so, the Hand position and the Auto position require discrete inputs to the control system.
7. Apart from this I have considered few DI's for MCC Incomer's open or closed status.
Is it about the status of MCC Main Circuit Breakers? Does each motor "bucket" have an auxiliary switch to monitor its status? If so, these are often wired to the "smart motor" so that their status is communicated via the network rather than using discrete inputs. This cuts down on "IO count", but does not cut down on "complexity".
8. Interposing Relays
Interposing Relays are used when the amperage requirements of the final motor starter coil exceed the available amperage rating of the "first line" output device. This is a function of the hardware and how you propose to control the motors and must be addressed on a case-by case basis.
You may also like:
Variable frequency technology is a new drive technology which adopts advanced electronic technique, computer control technique and communication technique. It goes ahead of any other speed adjusting methods. ...
Variable frequency drives manufacturers in the domestic market of more than 300. VFD supporting industries in China is relatively weaker domestic brands in terms of manufacturing, industrial design and other ...
say there is a permanent fault on overhead transmission line, the distance / line differential protection should operate and trip respect circuit breaker (CB) which is feeding the fault. This protection relay ...
Variable speed drives have come a long way in the past 20 years, from being a dumb component to intelligent process controller. Following are the main points to consider:
Advancements in industrial Ethernet switching technology have greatly improved the reliability in Ethernet communication. With the automation industry rapidly transitioning to Ethernet as a communication ...
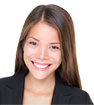
Hot Tags
Featured
7 months back I was involved in a harmonics evaluation study at Budweiser. This was one of many I've participated in over the past 20 years, basically because in facilities like ...
Most of variable speed drives are applying on high temperature fans, kiln head coal mill fans, kiln head surplus fans, raw mill circulating fans and so on. Two production lines ...
Variable speed drive application in purification system optimizes the system performance, improves purification effect, reduces power consumption greatly. According to related ...
The motor power factor does not make a big difference other than giving an idea of loading. In regards to the variable speed drive fixing power factor everyone is mostly correct. ...
A soft starter is a basic device which will ramp up the speed of your motor to full speed over a preset time, easing mechanical stress and also easing the high inrush currents ...
What's New
Variable Speed Drive Harmonics
Variable speed drive energy saving in cement industry
PLC and DAQ
Is it good to do preventive maintenance for variable speed drives
Does motor starts number affect motor life?
Variable speed drive for ID Fans in mining industry
Regenerative power frequency back to line power
Variable speed drive for axial-flow fans
Variable speed drive energy saving in cement industry
PLC and DAQ
Is it good to do preventive maintenance for variable speed drives
Does motor starts number affect motor life?
Variable speed drive for ID Fans in mining industry
Regenerative power frequency back to line power
Variable speed drive for axial-flow fans