The motor power factor does not make a big difference other than giving an idea of loading. In regards to the variable speed drive fixing power factor everyone is mostly correct. A variable speed drive will always show a DPF (Displacement Power Factor) near unity. DPF is what a utility company traditionally monitors and is the measure of lag looking at current and voltage of power at 60hz or fundamental only. The true power factor on a VFD will change with loading etc and includes current and voltage inclusive of harmonics.
Theoretically a system that is based VSD should have the right to be named servo system just when it has a feedback system that is connected to the load. I've read a lot of comments were the word servo is associate to high performance. I have to say that on a lot of industrial drives, the micros that are handling the closing of the current and speed or position loops, are nicer in drives that are typically sold/specialized for PM motors.
From an amplifier design standpoint, the Safe Torque Off (STO) is redundant with the enable input to the amplifier. I'm not sure what "problem" this STO requirement is trying to solve that the enable/disable doesn't solve, unless there's some variable speed drives out there that don't implement the enable/disable correctly and tend to take off when not commanded.
The VSD main advantage is saving electricity, saving rate depends on the application and running time.
The other advantage is protecting the electric motor, you can see if a high power machine start, other machines will be effected like low voltage.
After you use VSD to control the motor, the power grid line is more stable and no instantaneous current shock to the electric motor.
It is possible to power a three phase motor from a single phase power supply and using a capacitor bank to create the rotating magnetic field. Basically the capacitor banks ensures that there is a phase difference between the current and the voltage.
VFD is for controlling the speed of a motor which is under load, by changing the frequency of applied voltage. When your production line needs the motor to produce lower power, with the same torque it had before, its speed should be lowered by decreasing the frequency of applied voltage, this makes the impedance of the motor decrease and in turn, the amount of applied voltage comes lower and power consumption comes lower.
Even with a constant speed you will have to start and stop the motor. If you just have an IGBT power block producing a fixed frequency you will have to deal with the high inrush current, 3-5 times FLA. The are several companies that make chassis or open style VFDs that can be around 30% less than the standard IP20 versions with all the fancy stuff.
Contact the local variable frequency drive distributors and see if there are any classes on VFDs you can attend. These are periodically given by there various manufacturers to promote the use of their brand. If you have a particular application the distributor may show you how to do it with their brand of drive. You can also go on various manufacturer web sites and go through the technical support library.
A soft starter is a basic device which will ramp up the speed of your motor to full speed over a preset time, easing mechanical stress and also easing the high inrush currents which can be experienced by starting a motor under load. A breaker will cut the supply to your motor if the load is too high. A VFD will allow you to control a motor (to varying degrees of accuracy depending on the model selected) by varying the phase angle (amongst other things). It will give you the most control over your motor including at the most basic ramp time running speed.
How to measure or diagnose common mode voltage of three phase PWM variable speed drive? And how to solve EMI from motor Driver?
For your first question: Could you let me know your definition of variable speed drive "common mode"? Is this the voltage between one phase IGBT leg and the neutral point of stator "Y" connected machine?
For your first question: Could you let me know your definition of variable speed drive "common mode"? Is this the voltage between one phase IGBT leg and the neutral point of stator "Y" connected machine?
Instead of using brushes, I have been using either a sine wave filter or a dv/dt filter at the output of the variable speed drive. A sine wave filter eliminated all the high frequency from the VFD output and I have very good luck with that implementation -- have not seen bearing burn out. When using dv/dt filter, I like to keep the dv/dt below 200 volt / micro-second. The dv/dt filter design must have the common mode capability.
Converting a synchronous motor to an induction motor is easily done, to most motors, by shorting the rings, however, you would most likely need to use a properly sized VFD to get the starting torque you need. If you are interested to do such an upgrade you should consider the age of the motor and any other peripherals (gearbox, etc.) in the drive train.
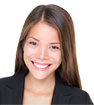
Hot Tags
Featured
7 months back I was involved in a harmonics evaluation study at Budweiser. This was one of many I've participated in over the past 20 years, basically because in facilities like ...
Most of variable speed drives are applying on high temperature fans, kiln head coal mill fans, kiln head surplus fans, raw mill circulating fans and so on. Two production lines ...
Variable speed drive application in purification system optimizes the system performance, improves purification effect, reduces power consumption greatly. According to related ...
The motor power factor does not make a big difference other than giving an idea of loading. In regards to the variable speed drive fixing power factor everyone is mostly correct. ...
A soft starter is a basic device which will ramp up the speed of your motor to full speed over a preset time, easing mechanical stress and also easing the high inrush currents ...
What's New
Variable Speed Drive Harmonics
Variable speed drive energy saving in cement industry
PLC and DAQ
Is it good to do preventive maintenance for variable speed drives
Does motor starts number affect motor life?
Variable speed drive for ID Fans in mining industry
Regenerative power frequency back to line power
Variable speed drive for axial-flow fans
Variable speed drive energy saving in cement industry
PLC and DAQ
Is it good to do preventive maintenance for variable speed drives
Does motor starts number affect motor life?
Variable speed drive for ID Fans in mining industry
Regenerative power frequency back to line power
Variable speed drive for axial-flow fans