But, compare with imported variable frequency drives, China domestic VFD's technologies need to take some time to catch up. Although in recent years the use of localization VFD brands have some advantages, but in overall, the strength of China variable frequency drive's industries is still relatively weak. Despite technology, manufacturing, industrial design, or in financial, China domestic VFD brands still have a certain gap with foreign brands.
Therefore, such operation methods not only meet the heating requirements, improve operational efficiency, but also save lots of electricity energies. However, in those operation methods, it requires the variable frequency drive has speed tracking feature, particularly from the commercial power supply switches to variable frequency operation. Thus, the motor has a smooth switching when power supply cut off, from idle to restart, thereby enhance the system reliability and stability in continuous operation.
When choosing variable frequency drives for an application it's critical to know exactly the purpose intended. There are so many variables. A fan application although simple enough can have many factors that can complicate a motor if not correctly sized or programmed.
Most vector VFDs can handle a fan application but the key is selecting and sizing a drive for long term and that will pose no unwanted spikes or heat production on both electric motor and the VFD drive.
Most vector VFDs can handle a fan application but the key is selecting and sizing a drive for long term and that will pose no unwanted spikes or heat production on both electric motor and the VFD drive.
In fan application, should we run the variable frequency in vector control mode or v/f mode? what are the pros and cons of both the modes. what are the methods to find out the correct running of the motor?
It depends on the application. If it is a small fan or easy application go with V/F. As a rule V/F is going to be less accurate, lower current and less money. You can buy a vector VFD and run it in V/F mode.
It depends on the application. If it is a small fan or easy application go with V/F. As a rule V/F is going to be less accurate, lower current and less money. You can buy a vector VFD and run it in V/F mode.
If a guarantee is involved with stiff liquidated damages, then lots of testing and certification on each serial numbered unit is likely to be necessary. (not to mention the cost of law suits....). Like the supply of a nuclear reactor: the reactor is free, it is the paper work that costs billions.
What motor rating is used is determined by the amount of torque required to move the load. Horsepower does not move the load, torque moves the load. A 1-hp, 6-pole motor will develop 50% more torque than a 1-hp, 4-pole motor If the manufacturer of the agitator is provided with the density of the material beforehand they should determine what torque is required and supply a motor to suit.
1a. if the driver is a synchronous motor there isn't a power factor problem as the motor will be either 1.0 or leading PF
1b. if the driver is induction: check with the motor manufacturer for the power factor vs. load curve AND request from the manufacturer of the recommended maximum PF correction capacitor.
2. If it is a variable frequency drive, check with the VFD manufacturer to see what kind of front end it has, and then validate what the vendor can allow as PF modification equipment placed before the AC drive.
1b. if the driver is induction: check with the motor manufacturer for the power factor vs. load curve AND request from the manufacturer of the recommended maximum PF correction capacitor.
2. If it is a variable frequency drive, check with the VFD manufacturer to see what kind of front end it has, and then validate what the vendor can allow as PF modification equipment placed before the AC drive.
The real facts which determine the usability of anti-friction or sleeve bearings: low coast over a long period; cheaper periodic maintenance and/or reduced noise. Another important reason for the application of sleeve bearing is the rotor dynamic design.
On electric drive large NG compressors, inlet pressure 70 psi, outlet about 1100 constant torque, what about electrical load, especially the reactive component, is it dynamic or relatively static?
If it is a centrifugal compressor, and you are using the variable frequency drive only as a soft start, it behaves as a variable torque load.
If you use the VFD drive for flow control, there are areas of it being constant horsepower.
We are going to go with ac motors and newer variable frequency drives. Management is wanting to keep the Simatic S5 PLC. If we keep this plc do I need to have any programming changes done to the plc to recognize/communicate with the new VFDs? Will the Simatic S5 PLC be compatible with newer VFDs? Finally would it just be wiser to upgrade the plc? We are not upgrading the whole production line just the palletizing section of this production line. This production line makes paper bags.
Successful rewinding of motors that are driven by variable speed drives does not rest on one large issue but in several small issues, all must be taken care of. I can only hope that the invention of variable speed drive will lead us back to the days when rewinding was a skilled trade.
Most important is the starting torque of the motor, with the major difference, high starting torque motor or a normal starting torque motor. Depending on the type of load you need to accelerate you will select the motor accordingly. Compressors for example are normally a high starting torque application that will require the high starting torque motor.
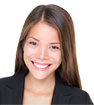
Hot Tags
Featured
7 months back I was involved in a harmonics evaluation study at Budweiser. This was one of many I've participated in over the past 20 years, basically because in facilities like ...
Most of variable speed drives are applying on high temperature fans, kiln head coal mill fans, kiln head surplus fans, raw mill circulating fans and so on. Two production lines ...
Variable speed drive application in purification system optimizes the system performance, improves purification effect, reduces power consumption greatly. According to related ...
The motor power factor does not make a big difference other than giving an idea of loading. In regards to the variable speed drive fixing power factor everyone is mostly correct. ...
A soft starter is a basic device which will ramp up the speed of your motor to full speed over a preset time, easing mechanical stress and also easing the high inrush currents ...
What's New
Variable Speed Drive Harmonics
Variable speed drive energy saving in cement industry
PLC and DAQ
Is it good to do preventive maintenance for variable speed drives
Does motor starts number affect motor life?
Variable speed drive for ID Fans in mining industry
Regenerative power frequency back to line power
Variable speed drive for axial-flow fans
Variable speed drive energy saving in cement industry
PLC and DAQ
Is it good to do preventive maintenance for variable speed drives
Does motor starts number affect motor life?
Variable speed drive for ID Fans in mining industry
Regenerative power frequency back to line power
Variable speed drive for axial-flow fans