In theory variable speed drive (VSD) is able to reduce the motor starting current at very low values is a fact that motor has limitations. I have seen many motors to stall because someone limited the starting current to a very low value. That low value is an argument to sell the equipment. Limiting the starting current depends on the type of motor and load operation curve reflected at motor shaft, for example a pumping system has a different curve than a conveyor and each application needs different starting torque and current.
It has no issues using an oversized VFD. Assuming that's a voltage source drive (most common topology). This design manages the voltage and frequency to attain commanded speed. The current supplied to motor is only what is needed to magnetize the windings plus the torque producing current. In other words, the VFD is a 'current allower' and not a 'current pump'.
As far as running two cables for reliability, the problem is that the failure of one parallel set of conductors reduces the available current to the motor, preventing it from starting. If you are seeking parallel redundancy, each triplex or set of three phases of conductors needs to be sized to carry the full load.
For instance, let's take a transformer for an example. You test a transformer and you get short-circuit and open-circuit impedances and losses. Then, the most basic model for such transformer is a T circuit, with series RL impedances (R and X) for each winding, with a central magnetizing shunt branch usually represented by parallel-connected R and L (G and B for their conductance and susceptance, respectively).
The proper operation of an AC system requires magnetization/energization of the apparatus, machines, transformers, lines, etc.
If you do not properly energize the equipment, no active power conversion, MW conversion, (mechanical power being converted to electrical power in generators, electrical power being converted to mechanical power in motors, etc.) can happen. Similarly, you cannot transfer active power from one winding of a transformer to another winding, without first building up the magnetic flux at the core of said transformer.
If you do not properly energize the equipment, no active power conversion, MW conversion, (mechanical power being converted to electrical power in generators, electrical power being converted to mechanical power in motors, etc.) can happen. Similarly, you cannot transfer active power from one winding of a transformer to another winding, without first building up the magnetic flux at the core of said transformer.
I think the reason why industry hasn't really latched onto it is because (unless you are using an IPM with a single large saliency) it really requires good knowledge of the particular motor saliencies, so it's not much use for general-purpose variable frequency drives (IPMs are not popular in general-purpose applications). However, for specific-purpose drives, it's very useful.
Most of the "bad press" for magnetic wedges comes from rewind shops, actually. Either the incorrect material is used (ranging from a poor magnetic profile to one that is not magnetic at all), or a bad match regarding mechanical strength is made (shape is wrong, or grain orientation is incorrect leading to poor retention of the coil, or the magnetic properties are damaged by the machining process, etc.)
For variable frequency drive in continuous operation, we take an external visual inspection for the VFD running state. Regular inspect variable frequency drive to see if there is running anomalies or not, we have following methods:
Control circuit provides control signal to the asynchronous motor power supply (voltage and frequency adjustable) main circuit, which has the arithmetic circuit of frequency and voltage, the voltage and current detection circuit of the main circuit, the speed detecting circuit of the motor, the driving circuit of the operation control signal amplifier, and the protection circuit of the inverter and motor.
Altitude Standard motors are designed to operate below 3300 feet. Air is thinner and heat is not dissipated as quickly above 3300 feet. Most motors must be derated for altitude. The following chart gives typical horsepower derating factors, but the derating factor should be checked for each motor. A 50 HP motor operated at 6000 feet, for example, would be derated to 47 HP, providing the 40°C ambient rating is still required.
A motor manufacturer assigns a RATING to the motor, which is put on the motor rating plate.( OR IN THE CATALOG)
As the rating plate mentions RATED output and RATED speed, RATED torque is derived from these.
As the rating plate mentions RATED output and RATED speed, RATED torque is derived from these.
Derating, in general, is a little misunderstood. If a motor and variable frequency drive is in the same relative environment, derating of the variable frequency drive is not required. If you have a 10hp motor and VFD at sea level and then move them to, say, 10,000 feet, they derate together, so they still work together.
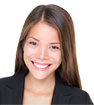
Hot Tags
Featured
7 months back I was involved in a harmonics evaluation study at Budweiser. This was one of many I've participated in over the past 20 years, basically because in facilities like ...
Most of variable speed drives are applying on high temperature fans, kiln head coal mill fans, kiln head surplus fans, raw mill circulating fans and so on. Two production lines ...
Variable speed drive application in purification system optimizes the system performance, improves purification effect, reduces power consumption greatly. According to related ...
The motor power factor does not make a big difference other than giving an idea of loading. In regards to the variable speed drive fixing power factor everyone is mostly correct. ...
A soft starter is a basic device which will ramp up the speed of your motor to full speed over a preset time, easing mechanical stress and also easing the high inrush currents ...
What's New
Variable Speed Drive Harmonics
Variable speed drive energy saving in cement industry
PLC and DAQ
Is it good to do preventive maintenance for variable speed drives
Does motor starts number affect motor life?
Variable speed drive for ID Fans in mining industry
Regenerative power frequency back to line power
Variable speed drive for axial-flow fans
Variable speed drive energy saving in cement industry
PLC and DAQ
Is it good to do preventive maintenance for variable speed drives
Does motor starts number affect motor life?
Variable speed drive for ID Fans in mining industry
Regenerative power frequency back to line power
Variable speed drive for axial-flow fans