1. Slip energy recovery with the current motor but with dual inverter on rotor side, which may not be too expensive as it is lower power on rotor side and no change in motor.
2. Slip ring motor with shorted slip ring and stator side inverter control, which may be expensive due to higher cost of electronics for the higher power rating of stator side.
3. Sq cage motor with stator side inverter control, which may be expensive because of motor replacement and higher cost of electronics for the higher power rating of stator side.
2. Slip ring motor with shorted slip ring and stator side inverter control, which may be expensive due to higher cost of electronics for the higher power rating of stator side.
3. Sq cage motor with stator side inverter control, which may be expensive because of motor replacement and higher cost of electronics for the higher power rating of stator side.
A good motor with a good variable frequency drive can give 100% of nominal torque at 5% of rated speed, and sometimes at such speed torque should be also higher. If possible, take care to increase cooling not only by convection in air, but also by conduction to cool metal base or metal flange. You can also increase infrared emission using a treated motor surface to increase heat emission (Alumite finishing, or some black paints or treatments).
One of the ways these days that i check this process is by observing the winding process. By understanding the winding environment and not assuming anything, By taking part actively in DFM. By seeing what happens in production and making changes that seem easy to me but may seem very difficult to people on the floor.
It involves my proprietary power electronics, DC machines working in concert with AC grids, bi-directionally blocking the traditional amp draws of the AC grid and bi-directionally permitting forward emf generation as the DC machine armatures rotate counter clock-wise at their drive ends. All working in concert with each other to perform useful work under load as negative electricity powered electric engines. The torque dynamics are all the mirror image of traditional torque dynamics, because we have discovered that "rotational thrust" is "relative" in terms of its action and reaction effects.
Another cause assuming reduced voltage start, star/delta, autotransformer, primary resistance, soft start etc., could be that the motor is not delivering torque sufficient to accelerate the connected load to speed. That is the starting current and starting time under RVS conditions exceeds that permissible by the overload curve. A more advanced protection strategy such as motor thermal modeling may be required. Motor thermal modeling allows the user to 'match' the curves of the protection device to the connected motor.
Actually, AC motor can be also applied with the used of AC Drive, Frequency Inverter. However, based on my actual encountered of almost different type of motors, from fractional size to medium voltage size, from various Manufacturing Industries particularly in Cement Plant, you have to oversize the AC Motor to match the torque carried by the DC Motor.
When select the CT ratio of 50/1 A for 6.6 kV drives where the SC rating of system is 40 kA, 50 protection may not operate because of CT saturation. Again, if the CT is not saturated, the relay terminal may not withstand the current >100 A (for 1 A sec). In case of 50/1 CT, for a fault current of 40 kA, the CT secondary will be having a current of 800A.
There will be little fall in the running torque supplied by the motor within the working voltage range of the motor and so the mechanical output and hence the electrical input remains practically same. The constant power concept is for practical purposes, as a thumb rule for frequency control like by variable speed drive.
If you are trying to switch faster than 1 microsecond your physical layout is essential. You should have a ultrafast freewheel diode as close to the IGBT as you can get it. Even if you think your load is resistive your wires , traces etc are not. THEN, your gate drive has to be very stiff. You have to hold it off when it switches off and the gate tries to follow the collector due to miller capacitance.
Due to current decrement in the Generator during fault conditions the Back-up protection with IDMT relay for a generator in the Electrical protection Scheme becomes complicated. Accordingly, the setting of the associated IDMT relay is set in such way that the said relay will not operate for a system fault but will respond when fault current is fed into the Generator which acts as a back-up to the main Generator Protection.
Through transformer you have flows of active and reactive power on their way to consumer, so you need to know quantity of power (active and reactive) which flows through transformer.
Comparision about AC 4 quadrant drives and hydraulic couplers application for downhill conveyors.
1. Energy saving
4Q drives boast perfect energy saving goal, can reach high power factor up to1, with energy feedback functions, regeneration energy can be returned to main supply, low heat loss of 1%.
Hydraulic couplers feature low energy saving effect, will waste 75% of energy at low speed.
1. Energy saving
4Q drives boast perfect energy saving goal, can reach high power factor up to1, with energy feedback functions, regeneration energy can be returned to main supply, low heat loss of 1%.
Hydraulic couplers feature low energy saving effect, will waste 75% of energy at low speed.
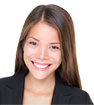
Hot Tags
Featured
7 months back I was involved in a harmonics evaluation study at Budweiser. This was one of many I've participated in over the past 20 years, basically because in facilities like ...
Most of variable speed drives are applying on high temperature fans, kiln head coal mill fans, kiln head surplus fans, raw mill circulating fans and so on. Two production lines ...
Variable speed drive application in purification system optimizes the system performance, improves purification effect, reduces power consumption greatly. According to related ...
The motor power factor does not make a big difference other than giving an idea of loading. In regards to the variable speed drive fixing power factor everyone is mostly correct. ...
A soft starter is a basic device which will ramp up the speed of your motor to full speed over a preset time, easing mechanical stress and also easing the high inrush currents ...
What's New
Variable Speed Drive Harmonics
Variable speed drive energy saving in cement industry
PLC and DAQ
Is it good to do preventive maintenance for variable speed drives
Does motor starts number affect motor life?
Variable speed drive for ID Fans in mining industry
Regenerative power frequency back to line power
Variable speed drive for axial-flow fans
Variable speed drive energy saving in cement industry
PLC and DAQ
Is it good to do preventive maintenance for variable speed drives
Does motor starts number affect motor life?
Variable speed drive for ID Fans in mining industry
Regenerative power frequency back to line power
Variable speed drive for axial-flow fans