Variable speed drive in China has nearly 20 years on the market, because of its good performance and considerable power saving effect, so in all walks of life in a very wide range of applications, so far has reached about 30% utilization rate. Especially in the last ten years, variable speed drive development is rapid, increase rate of every year is more than 20%.
With the continuous improvement of the technical level of textile machinery mechatronics, variable speed control has become a trend. Most textile machines apply variable speed drives in the AC induction motors.
Variable frequency drives manufacturers in the domestic market of more than 300. VFD supporting industries in China is relatively weaker domestic brands in terms of manufacturing, industrial design and other technical aspects with foreign brands there are some gaps. Currently, foreign brands in the domestic VFD market share of about 7 percent, products the local variable frequency drive enterprise main production of the V / F control, vector drives for superior performance, high technical content, the vast majority of domestic companies to develop products not mature enough.
Explaining some premature motor winding failures (multiple manufacturers) on VFD (multiple manufacturers) driven motors in high elevations. Some motors are VPI, all are inverter rated. Voltage varies from 460/480V - 575 and 690V. PWM varies from 1.5 - 3kHz. The failures are not seen at elevations below 3000M and the actual analysis of the failed motors are unreliable. Motors are appropriately derated for elevation in all cases.
Clarke and Park Transformation are "simply" matrix of transformation to convert a system from one base to another one:
- Clarke transform a three phase system into a two phase system in a stationary frame.
- Then Park transforms a two phase system from a stationary frame to a rotating frame.
- Clarke transform a three phase system into a two phase system in a stationary frame.
- Then Park transforms a two phase system from a stationary frame to a rotating frame.
SV-PWM is actually just a modulation algorithm which translates phase voltage (phase to neutral) references, coming from the controller, into modulation times/duty-cycles to be applied to the PWM peripheral.
It is a general technique for any three-phase load, although it has been developed for motor control.
SV-PWM maximizes DC bus voltage exploitation and uses the "nearest" vectors, which translates into a minimization of the harmonic content.
It is a general technique for any three-phase load, although it has been developed for motor control.
SV-PWM maximizes DC bus voltage exploitation and uses the "nearest" vectors, which translates into a minimization of the harmonic content.
The application will drive the choice of gear motor. If you go with brush DC motors you will save money but have a lot of maintenance. If you go brushless motor it costs more but last much longer.
The more detail you have about your application the better. Knowing exactly, in engineering terms, what your requirements are can save you a bunch of money.
The more detail you have about your application the better. Knowing exactly, in engineering terms, what your requirements are can save you a bunch of money.
Which method is better to drive this motor?
Trapezoidal control was discarded because of the ripple that affects motor torque (smooth movement desired). Now, is it sinusoidal control good enough or FOC control? Sinusoidal control has some problems with high rotation speeds, but, what is considered a high rotation speed?
Trapezoidal control was discarded because of the ripple that affects motor torque (smooth movement desired). Now, is it sinusoidal control good enough or FOC control? Sinusoidal control has some problems with high rotation speeds, but, what is considered a high rotation speed?
Someone wants to upgrade his tomato packing plant so he installs VFDs on the motors that have been in service since 1963 when they were first installed. Run them on the new variable frequency drives and they fail in 12 months, (almost) every time.
For simulink PMSM model, you'll have to determine if your motor is salient or non-salient one.. and other important parameters. Once you understand the Space-Vector theory you wouldn't even need the variable frequency drive (just generate the voltage vectors yourself), at least for first evaluation. however, if you do want to use the simpower blocks for the VFD, that'll be tricky (to connect the realized equations in simulink to simpower blocks).
The key to know which motor is better to use on variable speed drives depends entirely on the individual application for which it will be used.
The key to picking the proper motor based on the answers to these questions is to understand the difference between NEMA MG1 Part 30 which is titled "Application Considerations for Constant Speed Motors Used on a Sinusoidal Bus with Harmonic Content and General Purpose Motors Used with Adjustable-Voltage or Adjustable-Frequency Controls or Both" and NEMA MG1 Part 31 which is titled "Definite-Purpose Inverter-Fed Polyphase Motors".
The key to picking the proper motor based on the answers to these questions is to understand the difference between NEMA MG1 Part 30 which is titled "Application Considerations for Constant Speed Motors Used on a Sinusoidal Bus with Harmonic Content and General Purpose Motors Used with Adjustable-Voltage or Adjustable-Frequency Controls or Both" and NEMA MG1 Part 31 which is titled "Definite-Purpose Inverter-Fed Polyphase Motors".
In this case sometimes we recorded 775A as starting current and in other times we recorded 400 A for rotor current during start and for stator the current is variable, in some case it was 85 A, and in other was larger than 400a. This motor starts with liquid starter.
Questions: what is your idea about differentiation? What is cause of current reduction? Is the liquid starter resistance variable during each case of start?
Questions: what is your idea about differentiation? What is cause of current reduction? Is the liquid starter resistance variable during each case of start?
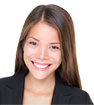
Hot Tags
Featured
7 months back I was involved in a harmonics evaluation study at Budweiser. This was one of many I've participated in over the past 20 years, basically because in facilities like ...
Most of variable speed drives are applying on high temperature fans, kiln head coal mill fans, kiln head surplus fans, raw mill circulating fans and so on. Two production lines ...
Variable speed drive application in purification system optimizes the system performance, improves purification effect, reduces power consumption greatly. According to related ...
The motor power factor does not make a big difference other than giving an idea of loading. In regards to the variable speed drive fixing power factor everyone is mostly correct. ...
A soft starter is a basic device which will ramp up the speed of your motor to full speed over a preset time, easing mechanical stress and also easing the high inrush currents ...
What's New
Variable Speed Drive Harmonics
Variable speed drive energy saving in cement industry
PLC and DAQ
Is it good to do preventive maintenance for variable speed drives
Does motor starts number affect motor life?
Variable speed drive for ID Fans in mining industry
Regenerative power frequency back to line power
Variable speed drive for axial-flow fans
Variable speed drive energy saving in cement industry
PLC and DAQ
Is it good to do preventive maintenance for variable speed drives
Does motor starts number affect motor life?
Variable speed drive for ID Fans in mining industry
Regenerative power frequency back to line power
Variable speed drive for axial-flow fans